Using Paper Forms Can Obstruct Data Collection During Preventive Maintenance
Using paper forms can be a hurdle for collecting and exploiting data during your preventive maintenance. The Ermeo tool allows you to organize these maintenance rounds and easily collect data.
With Ermeo, your field operator will have all necessary information at hand to perform their rounds confidently. They can also report any anomalies encountered during these rounds.
1. What is a Preventive Maintenance Round?
A preventive maintenance round is performed by a field operator based on criteria predetermined by a supervisor. With Ermeo forms, you can define these different criteria.
The objective of preventive maintenance is to reduce the likelihood of an asset's failure or the degradation of a service provided. It should also help prevent equipment failures in use.
By facilitating the visualization of information on the Ermeo application and allowing your operator to easily report information, you can reduce equipment downtime and anticipate corrective actions.
2. How to Implement Preventive Maintenance with Ermeo?
In this article, we will present the method to implement preventive maintenance rounds on Ermeo.
Example: Imagine an operator must perform preventive maintenance on all pumps at a site.
Here are the steps the operator will follow on Ermeo during their round:
- First, they will choose the site they are at.
- They will then get information about this site and their round. Next, a list of the pumps at the selected site will be displayed.
- For each pump, they will perform different inspections and can record data.
- If the operator detects an anomaly on a pump, they can report it. The anomaly will then be directly linked to the pump using the parent/child system.
3. Steps to Implement Preventive Maintenance Rounds on Ermeo:
- Create a Site Database: Create a database listing all sites where operators can intervene.
- Create a Pump Database: Create a database listing all pumps. Each pump will have its parent resource, the site it is located at.
- Create an Anomaly Database: Create a database listing all anomalies reported on the pumps. Each anomaly will have its parent resource, the pump it is found on.
- Create a Form for Maintenance Rounds:
4.1. In the form, load data concerning the intervention, the site, and the pumps at the site.
4.2. Allow the operator to report anomalies on inspected pumps.
Step 1: Create a Site Database
In this step, create a database to list all sites. Each site will be described by the following attributes:
- Client Contact (Text)
- GPS Coordinates (GPS Coordinates)
- Client Email (Email)
- Client Name (Text)
- Site Photo (Picture)
- Site Address (Text)
- Site Agency (Text)
- Site Access Instructions (Text)
- Site Contact (Action)
- Client Phone Number (Phone Number)
Ermeo allows you to create resources in bulk in a database using imports.
Your database will thus consist of various sites.
Step 2: Create a Pump Database
In this step, create a new database named "Pumps." This database will be described by the following attributes:
- Site/Location (Text)
- GPS Coordinates (GPS Coordinates)
- Date of Commissioning (Date)
- Serial Number (Text)
- Photo (Picture)
- Pressure (Number)
- Power (Number)
- Status (Multiple Choice)
- Type (Multiple Choice)
- Parent Resource -> Each pump will have a parent resource, which is the site where the pump is located.
Creating a new Pump asset in Pump database, it needs to be linked to the good parent site :
Step 3: Create an Anomaly Database
In this step, create a new database named "Anomalies." This database will be described by the following attributes:
- Site/Location (Text)
- GPS Coordinates (GPS Coordinates)
- Corrective Action (Text)
- Anomaly Creation Date (Date)
- Anomaly Handling Date (Date)
- Urgency Level (Multiple Choice)
- Anomaly Description (Long Text)
- Identified By (Text)
- Remains in Operation (Yes/No)
- Anomaly Photo (Picture)
- Anomaly Status (Multiple Choice)
- Anomaly Type (Multiple Choice)
Each reported anomaly will be described by a creation date, a description, a status, a photo, and a criticality level.
Step 4: Create the Form for Recalling All Pumps at a Site and Reporting Anomalies
The form created will allow the operator to perform the following steps:
1. In the field, at the start of the intervention/before beginning the intervention, the operator will select a resource that will be the main resource for the intervention. This resource will be the site of the intervention.
2. The operator will then obtain information about this site and the intervention. Next, the list of pumps at the chosen site will be displayed.
A site will be called at the beginning of the operation. All pumps related to the site will then appear.
3. For each pump, he will perform different inspections and will be able to collect data.
4. If the operator detects an anomaly on the pump, he can report it. The declared anomaly will automatically parent the pump containing the anomaly and will be stored in the "Anomalies" database.
Step 4.1: Creating the Form and Loading Intervention Information
- Create a new form and name it "Preventive Maintenance Round."
- Before starting the intervention from the app, the operator will select the site where they will intervene. This site will be present in the "Sites" database.
- In the editing studio, drag and drop a Section block widget and name it "Intervention Information."
- Inside this section, drag and drop a Text block widget.
4.1. In the default value of this Text block, place the User First Name and User Last Name tags and name it “Operator”.
4.2. Drag and drop another Text block and link it to the Client Name database attribute.
4.3. Drag and drop a Coordinates block and link it to the Site Coordinates attribute.
4.4. Drag and drop another Text block and link it to the Site Contact attribute.
4.5. Drag and drop a Phone block and link it to the Phone Number attribute.
Step 4.2: Loading Site Pumps
- Drag and drop an Auto-Selection block widget outside the "Intervention Information" section.
- Inside the Auto-Selection block widget, drag and drop a Date block widget. Link it to the Commissioning Date attribute.
- Inside the Auto-Selection block, drag and drop a Creation block. Select the "Anomalies" database in the Creation block settings.
- Inside the Creation block, drag and drop a Text block. Name this block "Declared Anomaly Description." Link this block to the "Anomaly Description" attribute.
- Inside the Creation block, drag and drop a Date block. Name this block "Today's Date." Link this block to the "Anomaly Creation Date" attribute
- Inside the Creation block, drag and drop a Multiple Choice block. Name this block "Anomaly Status."
- Publish the form.
- You can launch the form from the web app or the mobile app.
- Choose the site you want to work on. Verify the intervention information and select your pumps.
- Report your anomalies and then complete the intervention. The reported anomaly is now visible in your "Anomalies" database! The parent of the anomaly is the pump where the anomaly is found.
1.1. Name this block "Pump Verification." In the block settings, choose Parent is asset_name :
1.2. Sort by Number, then choose the Pump Number attribute.
2.1. Drag and drop a Number block and link it to the Pump Serial Number attribute.
2.2. Drag and drop a Multiple Choice block and link it to the Pump Status or Type attribute.
2.3. Drag and drop a Yes/No block and link it to the attribute "Is the equipment clean?"
5.1. Check the "Today's Date" option. By default, today's date will be entered.
6.1. Link this block to the "Anomaly Status" attribute.
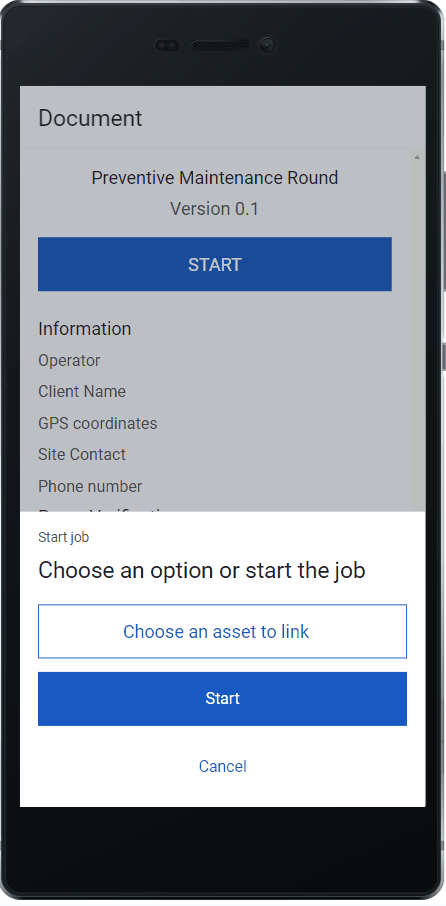
It is also possible to customize the name of the created anomalies.